Guidance and resources
Supporting your career and your business
We offer a range of guidance and resources to support professionals in their career and help businesses meet their occupational safety and health (OSH) obligations.
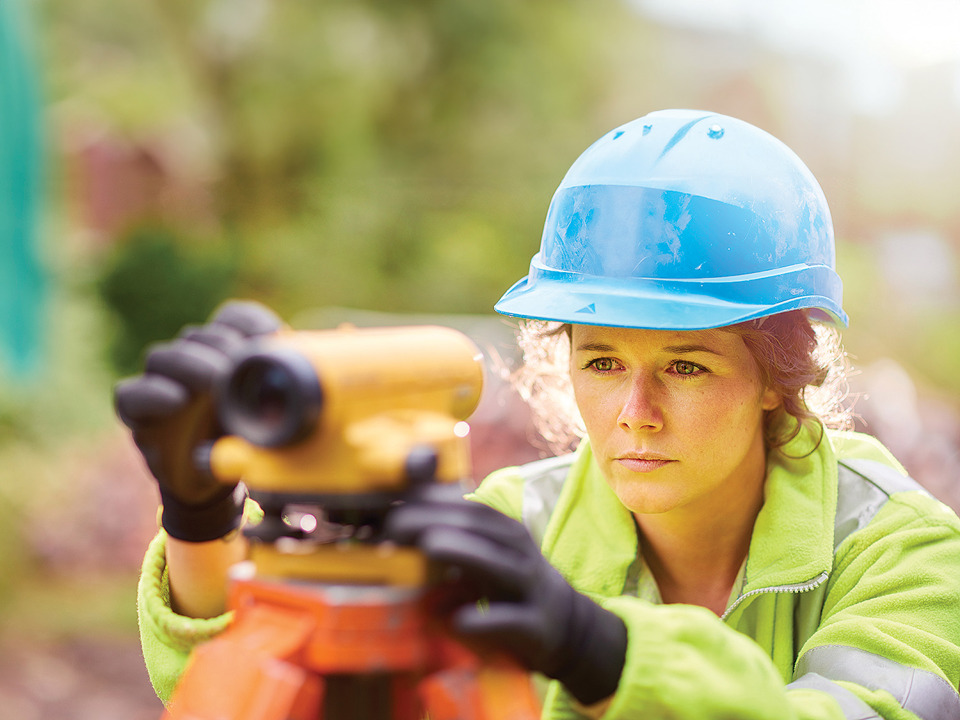
For OSH professionals
Whether you’re starting out or progressing your career, we can open up a world of opportunities to develop your skills and knowledge.
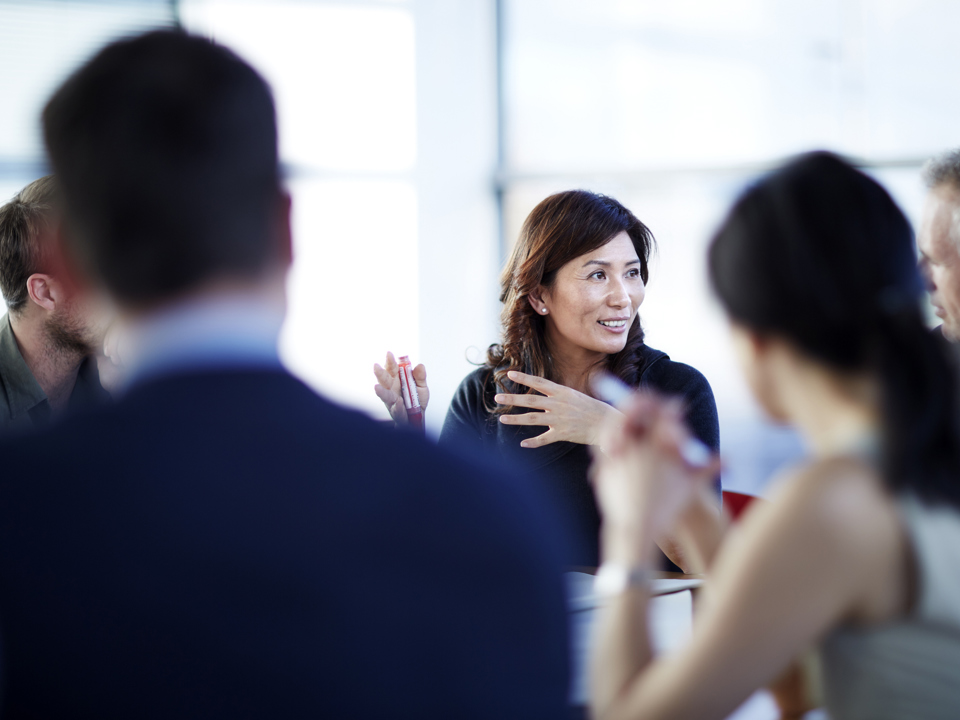
For businesses
Explore how to make work safer and healthier for your employees. Get expert guidance on your OSH responsibilities and the latest thinking within the sector.
Are you ready to fulfil your potential?
Blueprint is an all-in-one package available to members. It has everything you need to self-assess, learn and record your continuing professional development (CPD)